Acceleration is the rate of change of velocity, usually given in units of g. It is measured by accelerometers, which have the advantage of operating across a wide frequency range. Acceleration readings can be integrated to convert them into velocity, either in the accelerometer itself or in a subsequent signal processing stage.
The crest factor is the ratio of the peak value of a signal to its RMS value. For a sine wave, the crest factor is 1.414, while for a square wave it is 1.
Envelope g is a signal processing technique that uses spectral analysis of the signal envelope. It is useful for early diagnosis of bearing faults, since at this stage the impulses are often distributed over a very wide frequency range and can be masked by the machine’s rotational and structural vibration noise.
The constant-current accelerometer consists of a piezoelectric element with an integral charge amplifier built into a stainless steel housing. This is also known as an IEPE, ICP or sometimes two-wire accelerometer. It benefits from compact build and the requirement for only two cables which carry both power and signal. When a driving voltage of 24V is applied through a constant current diode the acceleration signal will appear as an alternating voltage. A further benefit of this drive system is that signal quality is not lost even for cable runs of several hundred meters. Even then any losses are confined to the higher frequencies which often do not contain significant vibration data and are anyway constant and so have little effect on vibration trend data.
A simple filter in the analyser circuit then yields a signal alternating around 0volts. All currently available portable vibration analysers and computer-based vibration systems will provide this type of drive. Where this power source is not available, then constant-current power supplies are available from Monitran to power the accelerometer and yield a clean AC voltage to your analyser or oscilloscope.
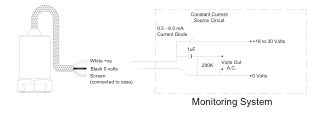
Constant-current accelerometer power and signal circuit
Some accelerometers are available with a voltage drive where for some reason constant-current operation is ruled out. In this case three wires are necessary and to avoid signal losses cable runs must be much shorter.
The most economic and versatile sensor for vibration measurements is the accelerometer. On rotating machinery these measure the radial forces on shafts and bearings. As the machine rotates a sensor fixed to the machine experiences a force on each revolution pushing or pulling it depending upon the orientation of the machine shaft. As the machine runs, a periodic vibration is observed at the sensor. The output of the sensor can be used to analyse the intensity and frequency of these vibrations which are a measure of the condition of the machine.
On moving objects, such as vehicles, or large structures such as tall buildings, towers or bridges, acceleration will not be periodic or, if so, it will be at very low frequency. In this case an accelerometer will still yield valuable data on the magnitude and time over which the forces are experienced or exerted.
Artificially created ground and building vibrations experienced during building, blasting, drilling or piling activities can also be sensed by accelerometers but as the vibrations are usually random the data must be acquired and analysed in quite different ways to allow sensitive vibration logging.
Natural ground vibrations, earthquakes and tremors are also detected by accelerometers built into measuring systems known as seismographs. Natural ground vibrations have long periods and generally require much higher sensitivities than machine vibration measurements and are outside Monitran’s scope of supply.
Shocks, such as experienced in crash, gunnery and explosive tests can also be measured by accelerometers though in this case there is usually a sudden deceleration at vehicle impact or acceleration at projectile release. The signal is transient over small fractions of a second but will be of very high magnitude. Sensors with very low signal filtering and optimised electronics are needed for this. Again, this is not a Monitran speciality.
Types of accelerometer
As with most technologies there are many ways a physical quantity can be sensed and there are numerous types of vibration sensor but for machine vibrations and many test and measurement applications piezoelectric and piezoresistive (strain gauge) sensors predominate.
Piezoelectric accelerometer
This commonly encountered accelerometer consists of a piezoelectric crystal held in compression by a known mass which when mounted on a machine is periodically compressed and re
laxed during each rotation. Charge in the crystal increases during compression and decreases during relaxation as force is periodically applied and released; generating an alternating current signal. This minute signal of only a few picocoulombs is then conditioned and amplified by either an internally or externally mounted charge amplifier to produce a useful alternating voltage for analysis. The accelerometer element alone can operate up to 250ºC without damage or severe loss of sensitivity while accelerometers with inbuilt amplifiers are limited to 125ºC or, in some cases, 140ºC maximum operating temperature.
- Vibration causes the mass to accelerate
- This produces a distorting force on the crystal
- The force on the crystal is proportional to the acceleration as F=ma
- Piezoelectric crystal produces a current proportional to the distorting force exerted
In this schematic you can see the elements of a general purpose internally amplified (IEPE) accelerometer
Piezoresistive accelerometer
In piezoresistive accelerometers the applied force during acceleration causes the deformation of a flexible element inside the accelerometer package that is built on an electronic microcircuit. This deformation or
strain is proportional to the force applied and hence again acceleration. This signal can be processing in an external strain gauge amplifier or built in voltage or current output amplifier.
Unlike the piezolectronic accelerometer however this type of accelerometer does not need periodic compression to generate a signal and can therefore respond to linear accelerations in vehicles etc and even responds to the 1g pull of gravity when mounted in the vertical plane.
In this schematic you can see the elements of a piezoresistive (strain gauge) accelerometer. The actual structure is microminiaturized within an electronic microcircuit.
As a machine rotates and vibrates the bearings, for example, experience periodic accelerations, for that is what vibration is. However, we could also measure the velocity or displacement that accompany these vibrations. At normal machine speeds displacement is too small to yield useful data though velocity measurements have some interesting properties.
Firstly, the alternating velocity signal at low frequencies often has higher sensitivity and better signal to noise than the acceleration signal for vibration analysis and so we can use sensors designed to output this alternating velocity signal. These are called piezoelectric velometers.
Secondly, if the AC signal is conditioned to give its RMS (average intensity) value then a simple DC signal is generated which is ideal for monitoring and control processes. Usually, this is presented as a 4-20mA signal proportional to the range of the sensor in mm/sec and accessible directly by a PLC or other industrial controller. No signal analysis or special power supplies are necessary and extended cable runs are possible, easily up to a kilometre with good quality cable. These are often called velocity transducers.
When an AC acceleration vibration signal is fed into an FFT (Fast Fourier Transform) circuit a full spectrum of vibration intensity against frequency can be obtained. This is called a frequency domain plot which is much more informative than the raw time domain plot seen, for example, on an oscilloscope. This will show major vibration peaks at the machine’s fundamental running speed and other vibration peaks at harmonics and sub-harmonics of it depending upon how well the machine is balanced and aligned. Additional peaks will appear at higher frequencies caused by the vibration of the rolling elements in the bearings which show evidence of bearing wear. This fingerprint yields, to the trained vibration engineer, a complete diagnostic of the machine’s current condition and how long it may be safely operated before maintenance, e.g. replacement of the bearings, will be necessary. In general it is the change in relative intensity of each of these vibration peaks with time that yields the most valuable information. This trend analysis is usually performed on data downloaded from a portable FFT vibration analyser with which regular vibration readings have acquired. This is then further analysed by downloading to a PC equipped with machine condition monitoring software. As the database of readings increases the engineer is able to observe patterns of vibration that improve wear and failure prediction. It is also possible to use on-line analysis with fixed sensors though these systems are relatively costly and used only on the most critical equipment whose unexpected failure would cause serious economic damage to the enterprise.
Monitran sensors are compatible with all popular makes of portable and on line analysers.
Standard industrial Monitran accelerometers are fitted with integral stainless steel over braided PTFE twin-core cable. This cable has a twisted pair of conductors, (power/signal & common) plus a shield which provides a high level of immunity to electrical interference when installed as recommended. This makes the cable ideal for most industrial applications.
Coaxial cables are also used though they have lower immunity to interference while they may be completely adequate in some situations such as the laboratory where high power machines are not in the vicinity. These cables work well with BNC and Microdot connectors and are used in a flexible coiled assembly for connecting portable analysers to sensors switchboxes. In miniature accelerometers coaxial cables are necessary as twin core cables, though superior, are too large and heavy.
Environment
To withstand the rigours of internal and external factory and works environments with elevated temperatures, humidity, oil and other chemicals plus rain and cleaning down with high pressure hoses requires a robust cable construction. Monitran’s standard cables use ETFE insulation for high temperature resistance and chemical inertness plus overbraiding with stainless steel mesh to protect against abrasion and wear.
The above cables are used up to 140ºC while perfluoroalkoxyethylene (PFA) insulation allows operation to 260ºC.
For long periods of immersion and operation down to 100m depth an external polyurethane coating over ETFE insulated cores with optional stainless steel overbraiding exhibits excellent water resistance and long life.
For lower temperature operation and less demanding environments like testing laboratories PVC insulated cables are acceptable and economical.
In the above examples the sensors are usually permanently mounted to machinery such that flexibility is not the most important criterion. However, for measurements with portable vibration analysers coiled, stretchable cable with PVC insulation offer convenience and economy.
The performance and reliability of results from vibration sensors depends critically on their electrical connection to the measuring system. Connectors and cables must be selected carefully to ensure optimum data collection, minimum signal interference and suitability for the working environment. Cables may be directly connected to the sensor or via a plug-in connector.
Factory environments demand cabling with high levels of noise rejection, protection from external electrical fields and radiofrequency interference. Where possible, cables will be twin-core shielded. The twin cores will be twisted together and carry the power/signal and return signals. However, where cable dimensions are too large to allow connection to small and miniature sensors then single core, screened (coaxial) cables are supplied.
Extension
Cables to constant-current and 4-20mA output sensors can be extended over long distances with no significant effect on signal quality. When connecting large numbers of sensors to a remote control room it is convenient and economic to combine the cables at a junction box and make the onward connection with multi-core cables. Each sensor needs its own pair while a common shield is acceptable.
Charge output sensors, however, have very low level signals and 10m should be regarded as a normal maximum length. Following charge amplification, though, extension may proceed as above.
Proximity sensors work on the eddy current principle. A proximity system consists of a matched probe, an extension cable and a driver. A high-frequency RF signal at 1 MHz is generated by the driver, sent through the extension cable and radiated from the probe tip. The tip consists of a precision wound copper coil inside a chemical and temperature resistant PEEK case. The tip is either mounted on a threaded stainless steel rod allowing easy gap adjustment on a bracket via two locking nuts or a flat, low profile mount.
Eddy currents are generated in the surface of the target, usually a machine shaft. The driver demodulates the signal and provides a modulated DC Voltage where the DC portion is directly proportional to gap (distance) and the AC portion is directly proportional to vibration. In this way, an eddy current transducer can be used for both radial vibration and distance measurements such as thrust position and shaft position.
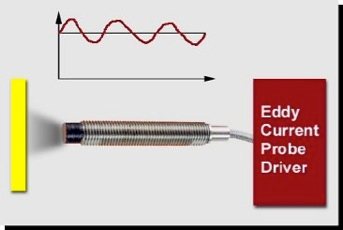
Eddy Current Transducers are calibrated at the factory for 4140 Steel unless specified otherwise. As eddy currents are sensitive to the permeability and resistivity of the shaft material any shaft material other than 4000 series steels must be specified at the time of order. In cases of exotic shaft material a sample may need to be supplied to the factory. Non-magnetic conductors such as aluminium or copper will show only around 50% of the linear working range of the standard steel calibration.
The RF field emitted from the probe tip of an eddy current transducer is in approximately a coned shape. Clearance must be provided on all sides of the probe tip to prevent interference with the RF field. As an example, if a bearing is drilled to permit installation, the hole must be counter bored to prevent side clearance interference. Care must also be taken to avoid collars or shoulders on the shaft that may thermally “grow” under the probe tip as the shaft grows from heat. There should be no conducting material level with the probe tip within three times its diameter.
The LVDT, Linear Variable Differential Transformer is a well established transducer design which has been trusted for many decades for the accurate measurement of displacement and within closed loops for position control.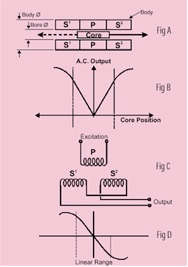
In its simplest form, the design consists of a cylindrical array of a primary and secondary windings with a separate cylindrical core which passes thought the centre. (Fig A) .
The primary windings (P) are energized with a constant amplitude AC supply at a frequency of 1to10kHz.
This produces an alternating magnetic field in the centre of the transducer which induces a signal into the secondary windings (S1 and S2 ) depending on the position of the core.
Movement of the core within this area causes the secondary signal to change (Fig B ) .As the two secondary windings are positioned and connected in a set arrangement (push-pull mode), when the core is positioned at the centre, a zero signal is derived.
Movement of the core from this point in either direction causes the signal to increase (Fig C). Due to the precise winding of the coils the signal output has a linear relationship with the actual mechanical movement of the core.
The secondary output signal is then processed by a phase-sensitive demodulator which is switched at the same frequency as the primary energizing supply. This results in a final output which after rectification and filtering gives a DC voltage. or 4-20mA current proportional to the core movement and also indicates its direction, positive or negative form the central zero point (Fig D).
The distinct advantage of using an LVDT displacement transducer is that the moving core does not make contact with other electrical components of the assembly and so offers little or no resistance to movement, high reliability and long life. Further, the core can be so aligned that an air gap exists around it, ideal for applications where minimum mechanical friction is required.
The crest factor is the ratio of the peak value of a signal to its RMS value. For a sine wave, the crest factor is 1.414, while for a square wave it is 1.
Envelope g is a signal processing technique that uses spectral analysis of the signal envelope. It is useful for early diagnosis of bearing faults, since at this stage the impulses are often distributed over a very wide frequency range and can be masked by the machine’s rotational and structural vibration noise.
A computerised procedure for calculating a frequency spectrum from a sampled time waveform. Used to produce a vibration signature.
Shock pulse is a signal processing technique that separates out the initial high frequency signal generated by the impact of metal-to-metal contact in bearings. It uses filtering combined with an accelerometer with specific characteristics for shock pulse measurement.
Triaxial sensors measure vibration in three axes simultaneously, enabling reduced measurement times. They also ensure the three readings are measured exactly at right-angles to each other.
Velocity is the change in displacement as a function of time, and is measured by velocity transducers. It is the time integral of acceleration, and can be derived from acceleration signals by integrating them.
The vibration signature of a machine is the characteristic pattern of vibration it generates while in operation, and is usually represented by the spectrum of the vibration signal.
A seismic transducer is one that measures absolute vibration, typically by generating a signal from the movement of an internal mass.
Analysis of the vibration of rotating or oscillating machinery can give an indication of current or future problems. Abnormal vibration can be caused by a wide range of issues, including shaft unbalance or misalignment, bent shafts, cracked rings, looseness, eccentricity, resonance, anti-friction bearings, journal bearings, fluid coupling or aerodynamics problems, oil whirl and other dynamic instabilities, gear or belt-drive problems.
Signal conditioning is the modification of a sensor’s signal by devices such as attenuators, filters and amplifiers to make it suitable for subsequent processing.
Condition monitoring is the process of monitoring the condition of machinery through the regular measurement of vibration or other parameters such as temperature or oil condition in order to identify changes that could indicate a developing fault. It is a major component of predictive maintenance.
A proximity probe or proximity sensor is a transducer that measures displacement. Commonly used to measure the variation in separation between a shaft and its support bearing.