When monitoring the operation of rotating shafts in pumps or turbines for example, it is important to use reliable non-contact sensors so changes in performance that could indicate future failure can be monitored. Andy Anthony, managing director of Monitran, outlines the benefits of using eddy current sensors for this type of application.
Eddy current displacement sensors are non-contact devices capable of high resolution measurement of the position of a conductive target. They detect the distance of the target by sensing fluctuations in the magnetic field generated by a reference coil in the tip of the probe.
The probe consists of a thermally stable plastic tip and when connected to a driver unit produces a high frequency oscillation that induces eddy currents in the target material. These eddy currents, and hence the oscillation amplitude, are proportional to the probe gap.
The driver unit contains the high frequency oscillator that drives the probe. Rectifying and linear circuits inside the driver convert the oscillator voltage from the probe into a DC voltage proportional to the gap. The driver unit is powered by a 24V DC supply and gives a positive output with respect to the power supply 0V. This DC voltage can be used for setting the probe to the correct distance from the target.
Target materials for eddy current sensors need to be conductive, but they can be magnetic or non-ferrous. The probe position should be chosen to minimise the effects of any surface roughness, changes in diameter or eccentricity, which will affect the accuracy of the measurement. The target area, perpendicular to the probe tip, must have a diameter of at least three times the probe diameter, with no discontinuities impinging such as spigots or keyways. In addition, no other metal parts should invade the area.
The driver unit can be mounted directly to the machine frame, or in a protective enclosure easily accessible to allow for setting-up. It should be sited away from sources of electrical interference such as large motors or inverters.
The sensors are rugged and able to operate over wide temperature ranges in contaminated environments that would be unsuitable for other types of devices. They have the advantage of being insensitive to the presence of non-metallic materials such as plastics and fluids in the gap between the probe and target. They are also less expensive than capacitive sensors and laser interferometers for example.
A range of types
Eddy current probes from Monitran consist of a precision-wound copper coil inside a chemical- and temperature-resistant tip. This is mounted on a threaded stainless steel rod for easy gap adjustment or on a flat, low profile mount. They are supplied with 1 metre of integral overbraided coaxial cable and operate up to 180˚C. An extension cable can be provided with a maximum length including the probe cable of 9 metres.
Current output drivers give a 4-20mA output directly proportional to the distance of the measured component and allow direct connection to PLCs and other industrial controllers. They can be used with any probe type.
Monitran’s most common probe for monitoring high speed pumps with plain metal bearings is the MTN/EP080, which has a diameter of 5mm and is able to measure small vibration levels with gaps up to 2mm. The MTN/EP200 is used to measure coarser vibrations and has a probe diameter of 13mm and an operating gap of up to 5mm.
Another popular probe is the MTN/EP340. Suitable for precision gap measurements in applications such as pump monitors, turbines and gauges, it has a probe diameter of 20mm and an operating gap of up to 8.5mm.
For the greatest protection from harsh industrial conditions, the heavy-duty MTN/EPHD80 eddy current probe system has a rugged IP65 cast aluminium driver housing with integral probe. The stainless steel probe sleeve is tailored to the exact insertion depth required and the probe can be exchanged without recalibration. It is particularly suited to thrust or vibration measurements on pumps and turbines.
Controlling the probes are drivers such as the MTN/ECPD/85, which is designed to monitor the axial displacement of a rotating shaft. The driver is powered from a 24V DC supply and provides a 4-20mA signal proportional to the gap between probe and shaft. It also has a DC voltage output, proportional to the gap.
Another driver from Monitran is the MTN/ECPD/60, which is designed to monitor the radial vibration of a rotating shaft. The standard range is 4-20mA representing 0 to 125μm peak-to-peak, but other ranges are available. The unit also has a DC voltage output, proportional to the gap.
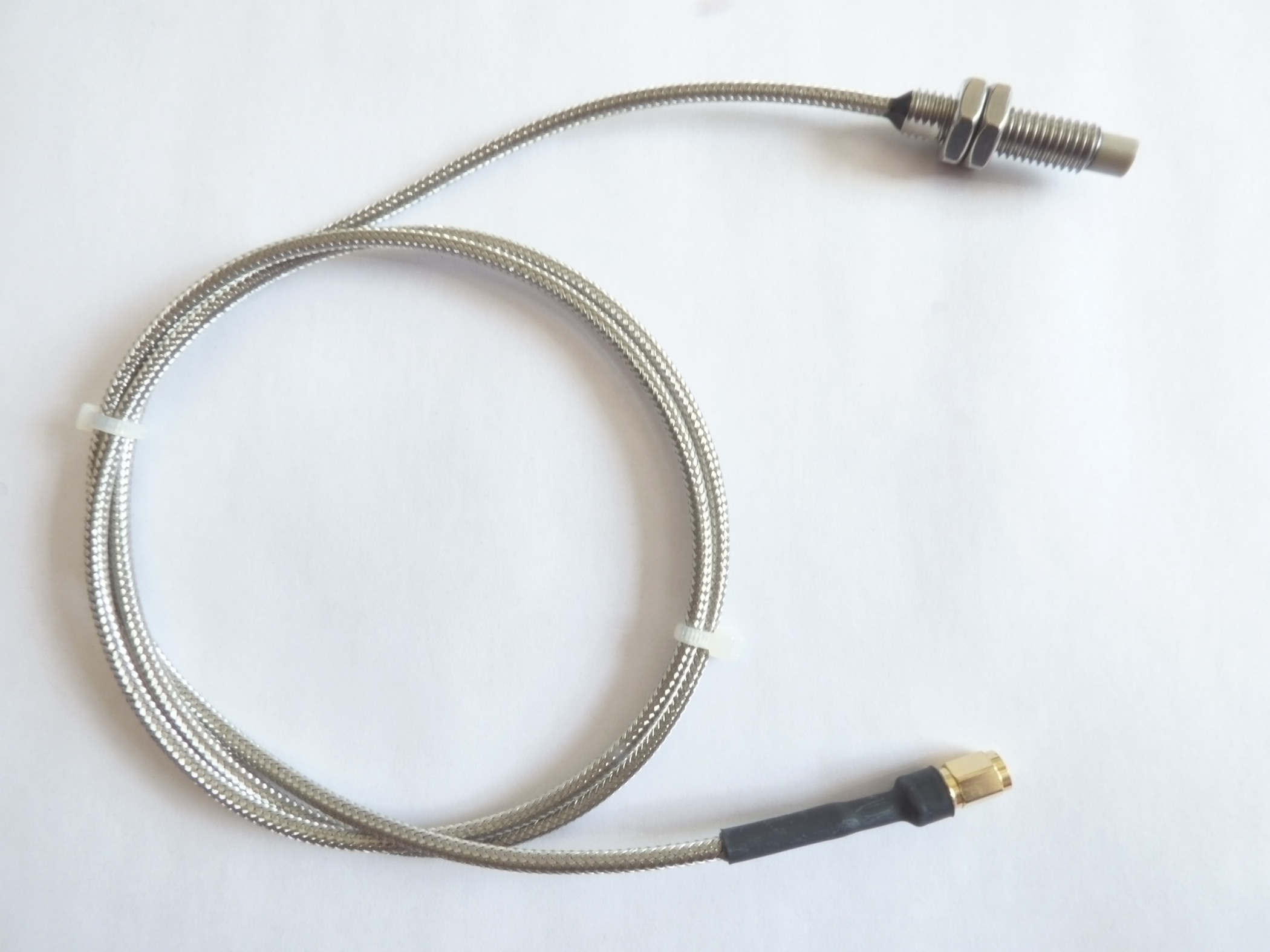
Image 1 The MTN/EP080 probe from Monitran has a diameter of 5mm and is able to measure small vibration levels with gaps up to 2mm.
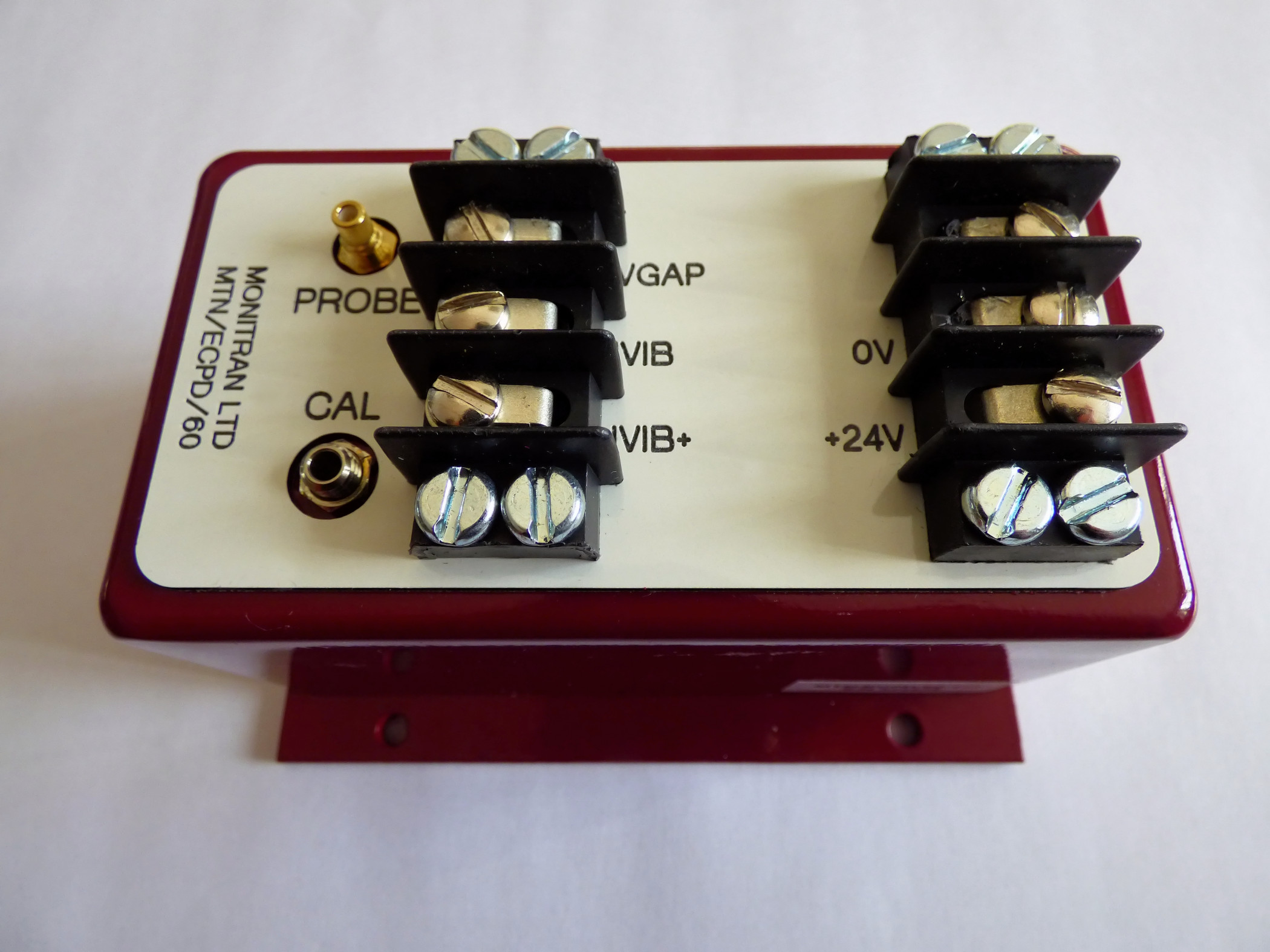
Image 2 The MTN/ECPD/60 driver is typically used when monitoring the radial vibration of rotating shafts.