Implementing continuous condition monitoring need not be as complex or as expensive as you might think. Andy Anthony, Managing Director of Monitran, explains why.
Monitoring the condition of machinery is a practical means of protecting plant and equipment against unexpected failure; as changes in vibration levels or temperature often provide the earliest indication that maintenance is necessary.
Vibration levels and temperature can of course be measured at regular intervals, using handheld instruments, and results recorded. However, it can be difficult to determine what the inspection intervals should be because component wear depends on usage (and load profiles with respect to time) and that will vary from machine to machine. Moreover, failures can still occur, even between close inspections.
There is then the matter of deciding how best to respond when a condition does change. For example, if an asset’s vibration levels are found to be higher than usual following a series of ‘normal’ readings you have no way of estimating when the levels started to rise? Just after the previous reading? Just before the current one?
For these reasons, continuous condition monitoring is highly recommended, particularly on machinery which, if it fails, could halt production and may even damage other equipment. There are some very advanced systems on the market which use complex algorithms to analyse vibration signatures and temperature changes in order to identify failing components automatically. Such systems require capital expenditure.
However, in most instances, all you really need is a) an indication that levels have changed, b) visibility of the rate at which the levels changed, and c) a means of automatically raising an alarm if predetermined levels are exceeded. Thankfully, all three goals are achievable with relative ease and well within a typical engineering/maintenance budget.
Sensing Changes
To monitor temperature and vibration, at the same time and location, dual output devices are available, which will simplify wiring.
To get the most from the sensors it will be necessary to ‘size’ each against the machine it is to protect, and we recommend the sensitivity of each sensor should be such that its output (or outputs if dual) will be about 80% of maximum when the machine on which they are mounted is operating under normal conditions. The use of handheld measurement devices, such as vibration meters, is recommended to establish the ‘normal’ levels, identify ‘start up’ levels and to identify where best to mount the sensors.
As for the condition monitoring system, ones like the MTN/5000 (see box) are affordable and easy to program when setting data sampling rates, input ranges and resolution and alarm levels. Regarding the alarm levels, if these are set too close to normal operating conditions you may get false alarms. Too high, and you run the risk of greater damage being done to the machinery before alarms are raised. During installation you will instinctively get a feel for what the alarm levels should be for each asset.
Once installed and operational, your condition monitoring system will provide a 24/7 ‘first line of defence’. You will be able to view historic data to determine at what rates conditions changed, and if raw signals are accessible you can connect a data logger or spectrum analyser for a closer look; as worn bearings, gears missing teeth and shafts out of alignment all have distinct vibration signatures.
If your condition monitoring system can be networked you will be able to feed data to a PC in order to develop your own condition-based predictive maintenance strategy. Plus, once the data is on a PC it can be made available online and accessible by engineers on call out.
Accordingly, your condition monitoring system can not only provide a 24/7 ‘first line of defence’ it can also become the core of something much more comprehensive.
Monitran
www.monitran.com
+44 (0)1494 816569
A picture of health
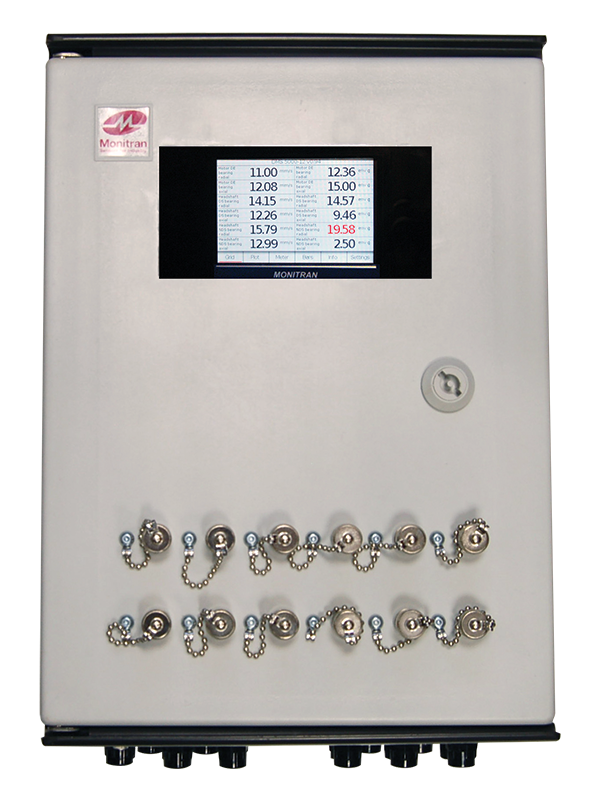
Launched at the 2014 Southern Manufacturing and Electronics show, the MTN/5000 (above) can have up to 12 channels and has a 3.5 inch TFT touchscreen and an easy-to-navigate menu. Data sampling rates (up to 1million/second), input ranges and resolution and alarm levels can be set on a channel-by-channel basis or across all channels.
Though designed to work with Monitran’s accelerometers and velocity sensors the system can also accommodate most other sensor types including those for measuring temperature, pressure, displacement and proximity. It can also accept a voltage or current as input, and raw signals are made available at BNCs on the front panel.
As standard, the MTN/5000 has 12 digital I/O channels which can be used for multiple alarms or as a communication channel for integration with other systems. Also, as an optional extra, the system can be fitted with Modbus TCP/IP, for networking purposes or to enable multiple MTN/5000s to operate together within a larger monitoring or control system.