By Andy Anthony, Managing Director of Monitran
Condition monitoring is essential if you wish to develop an understanding of the health and efficiency of a particular machine or process. Moreover, if the machine or process involves the use of motors, gearboxes or other moving parts, of all parameters that might be monitored vibration is arguably the most useful. Andy Anthony, Managing Director of Monitran, explains why and provides examples.
Within most applications in which components and sub-assemblies with rotating parts are employed, a change in vibration levels tends to provide the earliest indication that something is wearing or has broken. Also, as vibration is the movement of something, even if it is only air (i.e. noise), energy is being consumed, and if machinery – whether driven by electric motor, combustion engine or a turbine - is vibrating more than it should then it will undoubtedly be less energy-efficient than intended. In addition, analysis of the vibration signature can reveal the nature of the fault; for example, a broken gear tooth, a worn bearing or shaft out of alignment.
Vibration sensors are typically electronic devices, employing either piezoelectric or piezoresistive technology. Of these two technologies, the former is more prevalent in monitoring applications, and with no moving parts, a vibration sensor offers long-term reliability and stability.
Figure 1 shows a cut-away of a sensor. The mass is bonded to a piezoelectric crystal which, when placed under tension or compression, generates an electric charge proportional to the acceleration of the mass, and is the reason why vibration sensors are frequently referred to as accelerometers.
The electric charge is conditioned by the circuitry to produce a more useful output; typically DC in the range 4-20mA for ease or integrating the sensor into a monitoring system. However, sensors with AC outputs are also popular.
The output, proportional to acceleration in mm/s/s, may also be conditioned to represent velocity (mm/s) or displacement (mm), and sensors are also available with multiple outputs, e.g. acceleration and velocity. Typical frequency responses range from about 1Hz to 10kHz, though some sensors can measure down to DC (0Hz), for applications such as monitoring the movement of large structures such as bridges.
As for operating temperature ranges, even a general purpose sensor will cover -25 to 90oC. For high temperature applications, sensors are available that can cope with more than 200oC.
Best Picture
There are several different types of vibration sensor available on the market. If you are considering installing sensors as permanent fixtures onto machinery it will be important to make optimum use of the each sensor’s output range, without sacrificing its sensitivity. Many sensors are guaranteed by their manufacturers to operate across the range ±80g, though they can typically experience far greater forces without fear of damage.
Accordingly, if an AC sensor’s sensitivity is 100mV/g the output will swing between -8 and 8V across its declared operating range. However, if the sensor is likely to be exposed to no more than ±8g then it would be wiser to select a sensor with a sensitivity of 1V/g, as the output voltage swing will provide better resolution of the vibration levels.
As a rule-of-thumb, we recommend that any sensor’s sensitivity should be such that its output will be about 80% of maximum when the machine on which it is to be mounted is operating under normal conditions. As for gauging what ‘normal’ is, a handheld measurement device such as a vibration meter will help you establish not only the levels but also where best to mount the sensors.
With sensors in place, it is possible to start making use of the vibration level data. Here, it is worth recounting two very different condition monitoring projects, but both of which feature the 24/7 collection of data.
Hazardous Environment
During the construction of a new biomass power station in the north of England, the station’s operator identified the need to protect the site’s rail load-out system. It is used to transport fuel to the station’s burners and, in addition to rail carts, it includes hoppers, conveyors and feeders. The operator turned to Monitran and engineering reliability specialists Drive Management Services (DMS) to develop a conditioning monitoring system to interface with the site’s Supervisory Control and Data Acquisition (SCADA) system.
In designing the condition monitoring system, the companies determined that multiple assets should be monitored for rises in vibration and temperature levels; and that this could be achieved using 39 dual output sensors. In addition, the station’s main handling area is categorised as ATEX zone II, due to the fire and explosion hazards associated with biomass fuel. Accordingly, every aspect of the monitoring system in that area has to be intrinsically safe.
The sensors are permanently mounted on key assets which include motors, gearboxes, fan assemblies and bearing housings. In most cases they are then wired into local junction boxes, typically one per asset. Screened multicore cables then connect the local junction boxes to a wall-mounted microprocessor-based condition monitoring unit, located in the site’s Motor Control Centre (MCC).
The condition monitoring unit was built and pre-calibrated by Monitran and whilst the MCC is not an ATEX II zone, consideration had to be given to the fact that the unit is electrically connected to sensors which are in a hazardous environment. Zener barriers were employed, one per channel, to supress any voltages that could potentially cause a spark.
The unit has a 5-inch 800 x 480 pixel LCD screen, which is updated at five-second intervals and displays readings for the 78 channels (see figure 2), and connection to the site’s SCADA is via Modbus TCP Ethernet. The alarm level for each channel was set in the SCADA, on which a ‘look-back’ history can also be accessed to determine at what rate any of the conditions being monitored might be changing.
Following the installation and commissioning of the condition monitoring unit, realistic alarm levels were set in the SCADA; not too high, so that developing faults would go undetected for too long, and not too close to normal operating levels that false alarms might occur.
The ‘Virtual Engineer’
The second example to discuss, relates to the dairy industry and the bottling of milk. Stork Food & Dairy Systems is a keen advocate of condition monitoring; and condition-based predictive maintenance (CBPM), in particular. The company specialises in the development and support of integrated processing and filling lines for the dairy and other industries. It has 40 Dairyfill rotary fillers in use with UK-based customers.
The fillers typically operate 24/7 and are complex machines, operating at speeds of up to 300 2-litre bottles per minute. Shutdowns outside of scheduled maintenance have to be avoided.
In 2009, and working with the Institute of Industrial Research (IIR, now known as the Centre for Intelligent Data Solutions), Stork began developing an advanced condition monitoring system called ‘Virtual Engineer’; for which it received funding under the UK Government’s Knowledge Transfer Partnership (KTP).
Monitran made a site visit to see a Dairyfill machine in operation. Based on its observations and experiences from previous projects, it recommended the use of 16 mechanically mounted sensors per machine.
Stork’s engineers decided to monitor three fillers, fitted the recommended sensors and then used HBM data acquisition units, which can cater for up to 16 analogue inputs, to convert the sensors’ analogue outputs to 24-bit resolution digital. Data was sampled at a nominal 3kHz and streamed over the internet to the Centre for Intelligent Data Solutions. With such a high sampling frequency it was possible to build quickly a detailed picture of ‘normal’ behaviour, on a machine-by-machine basis and for different modes of operation.
During the first year of monitoring, anomaly detection algorithms identified six deviations from normal behaviour. Each was investigated and found to be developing conditions which, if left unchecked, would have led to a catastrophic failure. Interestingly, one of the faults was on a machine already protected by a third party complex spectrum analysis warning system. However, the fault was with a gear which rotates at about 7rpm, a frequency sufficiently low to be masked by the ‘noise threshold’.
A further eight conditions have since been detected. Also, Stork’s engineers observed some previously unseen spurious vibrations. These turned out to be a fault developing in a height adjustment system, which they had not set out to monitor. The discovery was good news, and it reinforced Stork’s conviction that, as time goes on and the clearer the picture of normal behaviour becomes, any new developing vibration patterns must be the tell-tale signs of a new fault.
Since the trials, vibration sensors have been fitted to a further eight fillers, which will be monitored using Virtual Engineer. As for the ROI? Based on the 14 failures that have been avoided, Stork estimates the savings are in excess of £2million. Also, Stork believes that Virtual Engineer marks the first use of a remote, real-time, asset monitoring system within a CBPM strategy built primarily around vibration levels and signatures in a dairy application, and possibly within the food and drink industry as a whole.
Do It Yourself
For monitoring the health of a machine or process, in most instances, all you are really after is a) an indication that levels have changed, b) visibility of the rate at which the levels changed, and c) a means of automatically raising an alarm if predetermined levels are exceeded. Thankfully, all three goals are achievable with relative ease and well within a typical engineering budget.
Condition monitoring systems, like the MTN/5000 (see box), are available which are easy to program, in terms of setting data sampling rates, input ranges and resolution and alarm levels. Once running, they can provide a 24/7 ‘first line of defence’.
www.monitran.com
Fig 1. Above, a cut-away of vibration sensor.
Figure 2. Above, the condition monitoring unit’s display (photo taken during commissioning) shows all 78 channels for the 39 dual output sensors.
Figure 3. Data collected from one of the Dairyfill machines being monitored. The light blue trace corresponds to vibration levels on the main gear box, which was found to be oscillating on its mount.
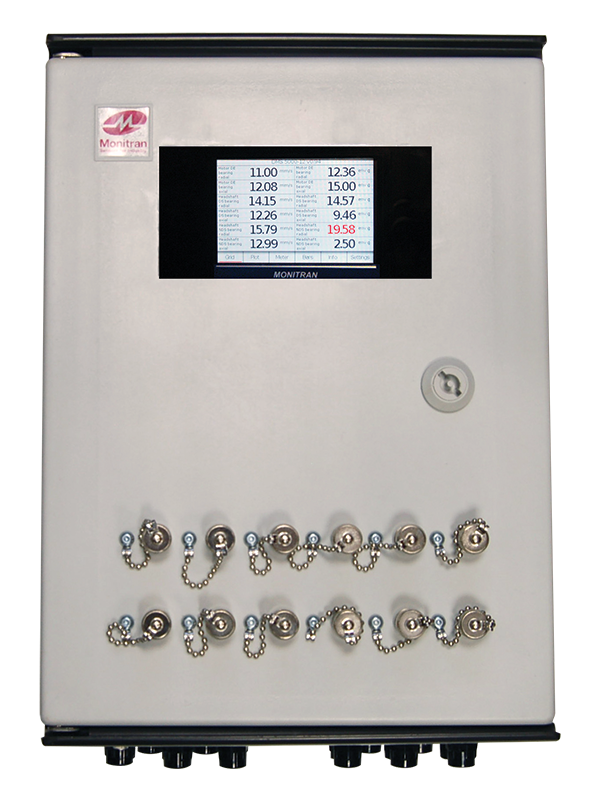
The MTN/5000 was launched at the 2014 Southern Manufacturing and Electronics show. It can have up to 12 channels and data sampling rates (up to 1million/second), input ranges and resolution and alarm levels can be set on a channel-by-channel basis or across all channels.
It works with most sensor types and can also accept voltage or current as input, and raw signals are made available at BNCs on the front panel. As standard, it has 12 digital I/O channels which can be used for multiple alarms or as a communication channel for integration with other systems. As an optional extra, the system can also be fitted with Modbus TCP/IP, for networking purposes or to enable multiple MTN/5000s to operate together within a larger monitoring or control system.
It’s Hard Life
Vibration-based condition monitoring systems are protecting the drivetrains of a number of the Indian Coast Guard’s hovercraft. Designed by Monitran, the system employs 14 general purpose constant-current analysis sensors (sealed to IP68) with AC outputs. These feed into a bulkhead mounted cabinet on which data is made available in different views. The cabinet also feeds a colour-coded status indictor (green for below threshold, red for above) in the cockpit to give the pilot an indication of drivetrain vibration levels.